一、優(yōu)化刀具管理
1.選用優(yōu)質刀具:選擇高品質、耐磨損的刀具,以減少刀具更換頻率和磨損對加工效率的影響。
2.刀具磨損檢測:定期進行刀具磨損檢測,及時更換磨損嚴重的刀具,保持刀具的鋒利和精度。
3.刀具預調和自動測量:通過刀具預調和自動測量技術,減少占機調整時間,提高加工效率和合格率。
二、制定合理的加工工藝路線
1.分析零件特點:在加工前,對零件的材料、結構特點和形位公差要求進行詳細分析。
2.優(yōu)化加工順序:根據(jù)零件特點選擇合適的銑削加工工藝和簡潔的加工路線,優(yōu)化加工順序,減少不必要的輔助時間。
三、加強數(shù)控車床的編程和管理
1.提高編程技巧:編程人員應熟練掌握數(shù)控車床的編程語言和編程技巧,編寫高效、簡潔的加工程序。靈活運用主程序和子程序,減少數(shù)控系統(tǒng)的累積誤差。
2.程序優(yōu)化:通過優(yōu)化程序結構,減少程序執(zhí)行時間,提高加工效率。
3.日常管理:加強數(shù)控車床的日常維護和保養(yǎng),確保設備處于最佳工作狀態(tài),避免因設備故障導致的生產(chǎn)中斷。
四、注重工裝夾具的應用管理
1.選擇合適的工裝夾具:根據(jù)加工需求選擇合適的工裝夾具,縮短工件的安裝和測量時間。
2.設計便于刀具交換的夾具:工裝夾具的設計應便于刀具交換,避免發(fā)生干涉碰撞,確保加工過程的順利進行。
五、靈活運用數(shù)控車床的各種輔助功能
1.刀具半徑和長度補償功能:利用數(shù)控車床的刀具半徑和長度補償功能,彌補刀具尺寸誤差,提高加工精度。
2.宏程序:通過運用宏程序,將有規(guī)律的形狀或尺寸用最短的程序表示出來,縮短程序編制和輸入時間。
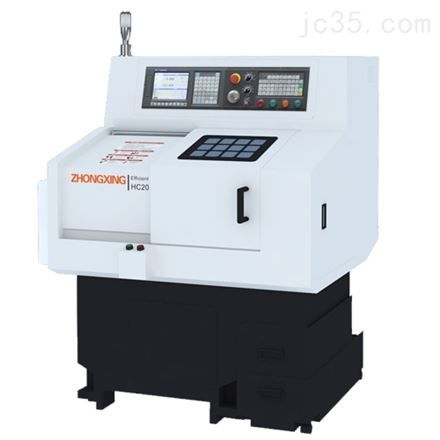
六、優(yōu)化加工參數(shù)
1.實時監(jiān)測加工參數(shù):通過實時監(jiān)測進給速度、主軸轉速、切削深度等加工參數(shù),操作人員可以隨時調整參數(shù)以提高加工效率和質量。
2.粗精加工參數(shù)選擇:在剛度允許的條件下,粗加工取較大的切削深度以減少走刀次數(shù),提高工件生產(chǎn)率;精加工則取較小的切削深度以獲得較高的表面質量。
七、引入自動化和智能化技術
1.快速換刀系統(tǒng):使用快速換刀系統(tǒng)可以大大縮短換刀時間,提高數(shù)控車床的加工效率。
2.自動化裝置:引入自動送料、自動夾緊裝置、自動測量裝置等自動化設備,減少人工操作時間,提高生產(chǎn)效率。
3.智能監(jiān)控:通過引入人工智能和機器學習技術,對加工過程進行實時監(jiān)控和預測,及時發(fā)現(xiàn)和解決潛在問題。
八、培訓與人員提升
1.提高操作者技能:數(shù)控機床的操作者是影響加工效率和質量的關鍵因素之一。通過培訓和實踐可以提高操作者的技術水平和經(jīng)驗判斷能力,使其能夠更好地操作和維護數(shù)控機床。
2.質量管理體系建設:建立完善的質量管理體系,嚴格執(zhí)行質量控制流程,確保加工過程的質量穩(wěn)定和產(chǎn)品的一致性。
提升數(shù)控平床身數(shù)控車床的加工效率需要從刀具管理、加工工藝路線、編程和管理、工裝夾具應用、輔助功能運用、加工參數(shù)優(yōu)化、自動化和智能化技術應用以及培訓與人員提升等多個方面入手。通過不斷優(yōu)化和改進這些方面,可以顯著提高數(shù)控車床的加工效率和質量。